Posted 25 July 2018 | By Cory Carter
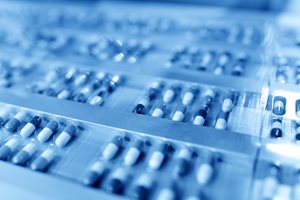
This article discusses current Good Manufacturing Practice (CGMP) requirements for companies making dietary supplements and who use contract manufacturers. The author highlights FDA comments on this issue, presents several court cases determining who is responsible for CGMP compliance and explains four important areas of CGMP concern for companies utilizing contract manufacturers. The author also offers ways to stay in compliance, such as auditing the contract manufacturer for CGMP compliance, establishing finished good and labeling specifications, identifying quality personnel and developing and implementing basic standard operating procedures.
Introduction
With the rise in US Food and Drug Administration (FDA) inspections, companies of all types are being audited for current Good Manufacturing Practice (CGMP) compliance, including companies who outsource all manufacturing, packaging, labeling and holding activities. In the current environment, companies in the dietary supplement industry utilizing contract manufacturers need to better understand their responsibilities and how FDA has chosen to enforce CGMP compliance.
Background
The Dietary Supplement Health and Education Act of 1994 (DSHEA) gave FDA authority to issue CGMP regulations for dietary supplements.1 The regulations were to be reflective of the 1994 CGMP regulations for foods, which were published in the US Code of Federal Regulations (CFR).2However, it was not until 2003 that FDA published the proposed regulations and they were quite different from food CGMP regulations.
The 2003 proposed CGMP rules were much more detailed and prescriptive than the somewhat benign food CGMP regulations. Over the following four years, numerous debates and opinions outlined the complexity of the dietary supplement industry. One of the most hotly contested topics surrounded defining exactly who is responsible for CGMP compliance. In 2007, FDA shared some comments surrounding this topic when their final rule was published.
“Some comments claim that a person who holds and sells packaged products should not be subject to dietary supplement CGMP requirements. Other comments state that dietary supplement CGMPs should apply to distributors as well as manufacturers. These comments assert many supplement distributors are merely marketers who employ contract manufacturers. The comments said that because marketers are the parties providing supplement to consumers, we should hold marketers responsible for their products and require marketers to ensure that their contract manufacturers adhere to CGMP requirements. These comments argue we should not permit marketers to transfer their responsibilities in delivering safe supplements…
Collectively, these comments raise a basic question as to which party or parties are responsible for complying with dietary supplement CGMP requirements where more than one party is involved in the manufacture, packaging, labeling, or holding of that dietary supplement.”3
Ultimately, FDA determined that all parties involved in manufacturing, packaging, labeling, holding or engaging contractors to conduct such services on their behalf are responsible for CGMP compliance. Of particular interest is how FDA addressed companies who sell a dietary supplement under their own company name, but contract out all manufacturing, packaging, labeling and holding responsibilities:
“In cases where a distributor contracts with a manufacturer to manufacture a dietary supplement that the distributor then distributes under its own label, the distributor has an obligation to know what and how manufacturing activities are performed so that the distributor can make decisions related to whether the packaged and labeled product conforms to its established specifications and whether to approve and release the product for distribution.”4
Enforcement/Warning Letters
Since the publication of the final CGMP regulations, FDA has issued Warning Letters to numerous companies who market dietary supplements, but rely on contract manufacturers to produce the products on their behalf. In these Warning Letters, FDA commonly cites the 2007 Federal Register notice, quoted above, indicating that because a company “introduces or delivers, or causes the introduction or delivery, of dietary supplements into interstate commerce in their final form for distribution to consumers…(the company) has an overarching and ultimate responsibility to ensure that all phases of the production of those products are in compliance with dietary supplement CGMP requirements.”5,6
In addition to the 2007 Federal Register, FDA relies on two cases as evidence that companies cannot contract out the ultimate responsibility of ensuring a dietary supplement is manufactured according to CGMP regulations. The first case is United States v. Dotterweich. In this case, Buffalo Pharmacal Company, Inc. and its president, Dotterweich, purchased drug products from a manufacturer and sold them under the Buffalo Pharmacal label. The court stated that “The offence is committed…by all who do have such a responsible share in the furtherance of the transaction which the statute outlaws – namely, to put into the stream of interstate commerce adulterated or misbranded drugs.”7,8
The second case, United States v. Park, addressed the topic of food safety concerns. A manufacturing facility was not complying with CGMP regulations and a senior officer in the company (Park) was found liable for the failure to comply with CGMP regulations, even though others within the company were specifically assigned the responsibility to oversee the compliance. In this case, the court stated that “corporate agents vested with the responsibility, and power commensurate with that responsibility, to devise whatever measures are necessary to ensure compliance with the (Food, Drug and Cosmetic Act).9
Both cases reference the responsibility of companies and individuals who may not directly oversee the production of a product. In both instances, individuals who were not directly involved were found liable for the activities because they should have implemented systems to ensure compliance with food and drug laws and regulations. FDA references these cases to emphasize the requirement of companies who hire contract manufacturers to ensure the contract manufacturer is producing the products in full accordance with CGMP regulations. FDA has taken this position further by referencing sections of regulations requiring production and process controls and quality control operations.
Production and Process Controls
Companies are required to implement a system whereby they ensure products are produced, packaged and labeled as specified in the master manufacturing record.10 This is not limited to contract manufacturers, but is also the responsibility of the company under whose name the product is sold, as reiterated in United States v. Dotterweich.
Quality Control Operations
Companies are required to establish quality control systems, “including written procedures for conducting a material review and making a disposition decision and for approving or rejecting any reprocessing.” 11 Companies who sell dietary supplements under their own name are required to make the final decision on whether to release product. This entails having quality control personnel take the necessary steps to ensure the dietary supplement product “is packaged and labeled as specified in the master manufacturing record.12 These processes require companies to maintain records that the quality control personnel in the company “approved for release, or rejecting, any packaged and labeled dietary supplement for distribution.”13
What do companies using contract manufacturers need to do?
To ensure all parties are in compliance with CGMP regulations, there are four important areas companies should consider when using contract manufacturers:
- auditing the contract manufacturer for CGMP compliance
- establishing finished good and labeling specifications
- identifying quality personnel
- developing and implement basic standard operating procedures
Auditing the Contract Manufacturer for CGMP Compliance
The purpose of an audit is two-fold. The first purpose is to determine whether a contract manufacturer is compliant with CGMP regulations. This requires the contract manufacturer to thoroughly understand their responsibilities under the regulations. The contract manufacturer should have standard operating procedures and documentation systems in place and should understand the importance of working with their customers to jointly meet regulatory requirements. Many contract manufacturers work to maintain certifications from industry bodies and will have reports of recent audits. It is always beneficial for companies to ask for recent audit reports and to review them to see if an outside auditor noted any non-conformances. If non-conformances were noted, companies should ask the contract manufacturers for evidence the non-conformances have been resolved.
Second, the purpose of an audit is to get the contract manufacturer to commit to provide all the necessary documentation needed to allow the company to meet its obligation to release products for distribution. This means the contract manufacturer must be willing to share batch production records, testing records and any other documents deemed necessary by the company to verify the product was produced according to the master manufacturing record.
Unfortunately, too many contract manufacturers are not aware of the responsibility of their customers when it comes to CGMP compliance. Many contract manufacturers do not want to share batch production records, testing records or standard operating procedures with their clients. Some manufacturers are not willing to share formulas or simply want their customers to accept a certificate of analysis as proof that a product meets regulatory requirements.
As noted previously, FDA requires companies engaging with contract manufacturers to make a material review and disposition decision prior to releasing a product for distribution. If a contract manufacturer is not willing to share documentation related to the production of the product, their client will not be able to properly verify the product was released according to the master manufacturing record and is, thereby, unable to comply with the regulations.
As with all aspects of regulatory compliance, an expert in CGMP regulations and supplier audits should be consulted and, if possible, should attend the audit. Having an independent representative for a company allows an un-biased audit to take place and can provide a realistic understanding of compliance of a contract manufacturer.
Establishing Finished Good and Labeling Specifications
Too often, companies rely on contract manufacturers to tell them what should be on the label or what specifications should be established for a product. However, if a product label is not compliant, or a product does not meet specification, the company under whose name the product is produced is ultimately responsible and will “pay the price” for non-conformance.
To illustrate the importance of establishing specifications, consider a company selling a powdered protein supplement. The contract manufacturer provides a suggested ingredient list, suggested usage instructions and a warning to “keep out of reach of children.” The main component of the product is whey protein, which the manufacturer accurately suggested should be listed as “whey protein” in the ingredient list. However, the manufacturer did not specify that milk should be declared in the ingredient list, nor did they indicate a warning was required because milk is an allergen. If the product is produced using the contract manufacturer’s proposed label text, and the product enters the market, the company will be forced to recall the product because an allergen was not declared. In this situation, the contract manufacturer is not named in the statements published by FDA, nor is the contract manufacturer’s name anywhere on the product. Consumers, newspapers and competitors will simply see the name of the marketing company, thereby negatively impacting their brand and company name, but not publicly affecting the contract manufacturer.
Establishing product and label specifications allows a company to maintain control of the product and ensure any assumed risk is a calculated risk. It also allows a company to go elsewhere if the contract manufacturer is not performing to the company’s expectations. Asking a contract manufacturer to make a product according to an established specification is much easier than asking a contract manufacturer to try to make a product based on a label provided by the previous manufacturer.
Identifying Quality Personnel in the Company
CGMP regulations require quality control personnel to ensure products are produced according to the master manufacturing record. In order to facilitate that review, quality personnel must be properly identified. When FDA conducts company audits, inspectors often will ask for an organizational chart. Within this chart they are looking to identify who is responsible for quality assurance and control. This is one of the primary indicators of whether a company understands the importance of having a functioning quality system.
Quality personnel are not required to be solely focused on quality. Many companies utilizing contract manufacturers are small and may only have a few employees. Regardless of size, someone in the company must be designated as the person ultimately responsible for ensuring quality parameters are met. This individual is responsible for reviewing batch production and testing records from contract manufacturers, developing product and label specifications and ensuring all other quality functions are properly operating.
Developing and Implementing Basic Standard Operating Procedures
Many companies do not realize that CGMP standard operating procedures and policies must be written and running when the company begins selling dietary supplements in the US. A company outsourcing all manufacturing, packaging, labeling and holding of dietary supplements is still required to have a CGMP program. It may not be as extensive as a contract manufacturer’s program, but there will be anywhere from 10–30 standard operating procedures and as many forms. Companies must identify policies and procedures for handling customer complaints, handling returned product, making material review and disposition decisions, establishing specifications, auditing and hiring a contract manufacturer, labeling (if kits or combination products are assembled by the company), sample retention, document retention, training, product destruction, quality control, record keeping and others.
In addition to writing procedures and creating the forms, the policies and procedures must be implemented. This requires training and filling out forms. Many companies will create procedures then stash them away in case of the “rainy day,” most likely the day FDA comes to audit them. FDA requires documentation to show the CGMP program is fully operating, so it is imperative that companies ensure product batches are being properly released by quality personnel, retention samples are properly marked and located, audit records are maintained and all other activities are properly recorded.
Summary
Utilizing contract manufacturers is the most feasible way to enter the dietary supplement market for many companies. However, the regulations are much more complex than simply asking a company to manufacture a product for you and offering it for sale on the internet. FDA is becoming more and more active in inspecting companies who outsource the entire production process and many of these companies are receiving Warning Letters for not complying with CGMP regulations. Once more, FDA has made it clear that they expect companies to understand their responsibilities and fulfill them, otherwise, there will be regulatory repercussions.
The key to avoiding potential issues is to understand the responsibilities, create the necessary documents and implement the program. Once implemented, a CGMP program is easily maintained, but it must first be developed. If companies are unsure of how or where to begin, there are many regulatory experts who can help companies develop and implement a CGMP program that will meet both regulatory and industry standards.
References
- 21 USC §342(g).
- 21 CFR 110.
- 72 FR 34789, 34790.
- Ibid.
- United States Food and Drug Administration, Warning Letter FLA-14-13, 29 May 2014, Bhelliom Enterprises Corp.
- United States v. Dotterweich, 320 U.S. 284 (1943).
- United States v. Park, 421 U.S. 672 (1975).
- Op cit 5.
- Federal Food, Drug and Cosmetic Act (FD&C Act). FDA website. https://www.fda.gov/regulatoryinformation/lawsenforcedbyfda/federalfooddrugandcosmeticactfdcact/default.htm. Accessed 20 July 2018.
- 21 CFR 111.55.
- 21 CFR 111.103.
- 21 CFR 111.105.
- 21 CFR 111.127(h).
About the Author
Cory Carter, MJ, CQA, is the founder of Carter Regulatory Group, an international regulatory consulting firm specializing in food, beverage, dietary supplement, cosmetic and OTC drug regulations. Carter has more than 15 years of experience in the dietary supplement industry and has represented many different types of clients in all aspects of US and international regulations. Carter frequently represents clients during FDA audits and in resolving FDA Warning Letters, form 483s. He holds a master’s degree in international food law from Michigan State University College of Law and is an ASQ Certified Quality Auditor. He can be reached at cory@regminds.com.
Cite as: Carter C. “CGMP Requirements for Companies Using Contract Manufacturers.” Regulatory Focus. July 2018. Regulatory Affairs Professionals Society.